Stuck spindles are not fun....
On our Thundercat and CHUGSzilla projects we removed all the spindles from the carriers. This was suggested by Tucker’s former parts and service manager Jeff Godard. Really, it’s preventive maintenance in case you ever have to change out a spindle in the field. Lying on your side, hopefully on a tarp and trying to swing a good sized hammer to beat the spindle out is a scenario I hope to never experience.
We did it in the comfort of Scott’s shop with a crane, a massive steel work table, oxyacetylene at the ready for heat, and a big hydraulic press. Even with all that... some of the spindles were downright recalcitrant. We eventually got them all out, and when it came time to reinstall them, they were liberally coated with anti-seize.
There is no magic bullet to get them out. In some cases (very few) it was just a few blows with about a three pound double jack. Others required the hydraulic press, some required heat, and still others required The Gorilla wailing away with a 12 pound sledge hammer. In the last situation you almost felt sorry for the spindle, the key word being “almost”.
I typically buy seals from Tucker, they used to be pretty reasonable cost-wise, but that was some time ago. They are a triple lip design and Tucker sources them from a company called Colonial Seal. If you elect to buy bearings and races from Tucker, you should know ahead of time they are made in China, and they aren’t Timken, Koyo, SKF or any other high quality bearing manufacturer. But think about it:
On your machine you have a total of 20 idler wheels and 40 tapered roller bearings. To make the math simple, let's say your Tucker weighed 8,000 pounds. That would be a load of only 200 pounds per bearing. And it’s not like Tuckers are fast, so the bearings don’t really spin very fast, either. In short, the task the bearings are required to fulfill is pretty minimal. The bearing size is very commonly used on boat trailers and you can find them quite cheaply.
It looks from the pics like your machine has an earlier design of grousers and perhaps the carriers as well. If the machine has a lot of hours on it, your journals may be worn. If so, I would encourage you to use what’s called bearing tape to essentially shim the journals to get them in alignment from the wear.
I think Track Addict was the first to do this, and we followed his lead with some work we did on a Tucker we re-cabbed known as the Vail Cat. They had broken the rear axle housing and we repaired that and did some other work. Here’s a link to that thread. You’ll have to scroll down a bit to get to the bearing tape posts.
Some months ago a new forum member started a thread inquiring about purchasing a used axle assembly for a Tucker with a broken axle housing. Reading the thread and looking at the photos revealed this was the machine Scott and I had re-cabbed and sold several years ago. Here's that machine.
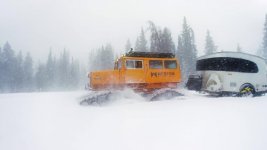
In addition to the cab modifications, we did a bunch of work to it - basically repairing anything and everything we found wrong. After talking with Scott, I made the offer that if you bring us the machine...